Art foundry
When first opened on quai de Conti in 1775, this workshop was dedicated to the manufacture of alloys and ingots for the manufacture of coins and medals. In 1973 the workshop devoted itself to the art foundry and it is today one of the last art foundries in activity right in the heart of Paris.
This workshop’s work includes the preparation of moulds, the pouring of the molten metal, the production of raw foundry bronze, chiselling and when the finish so requires, hot patinaing. The Art Foundry’s craftsman also have creativity and a sharp artistic sense
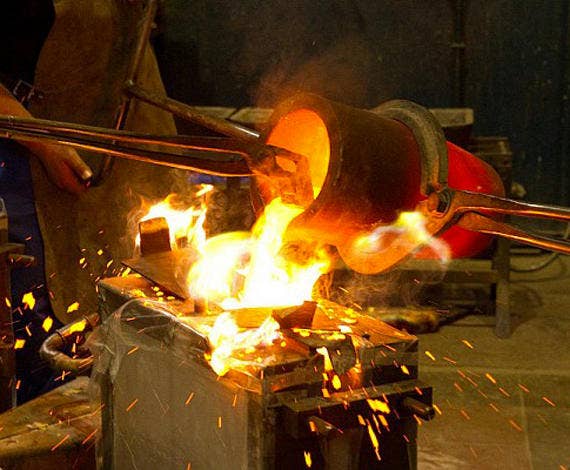
Teamwork
The first stage in the creation of an artistic bronze is the dialogue between the artist or the sponsor and the foundry’s craftsmen. The production is thought out in detail upstream of the manufacturing.
The technique chosen and the manufacture of the moulds are adapted to facilitate the finishing work and to enable the object to be magnified. Foundryman, chiseler and patiner anticipate potential irregularities or fragilities in the work to be produced from the outset.
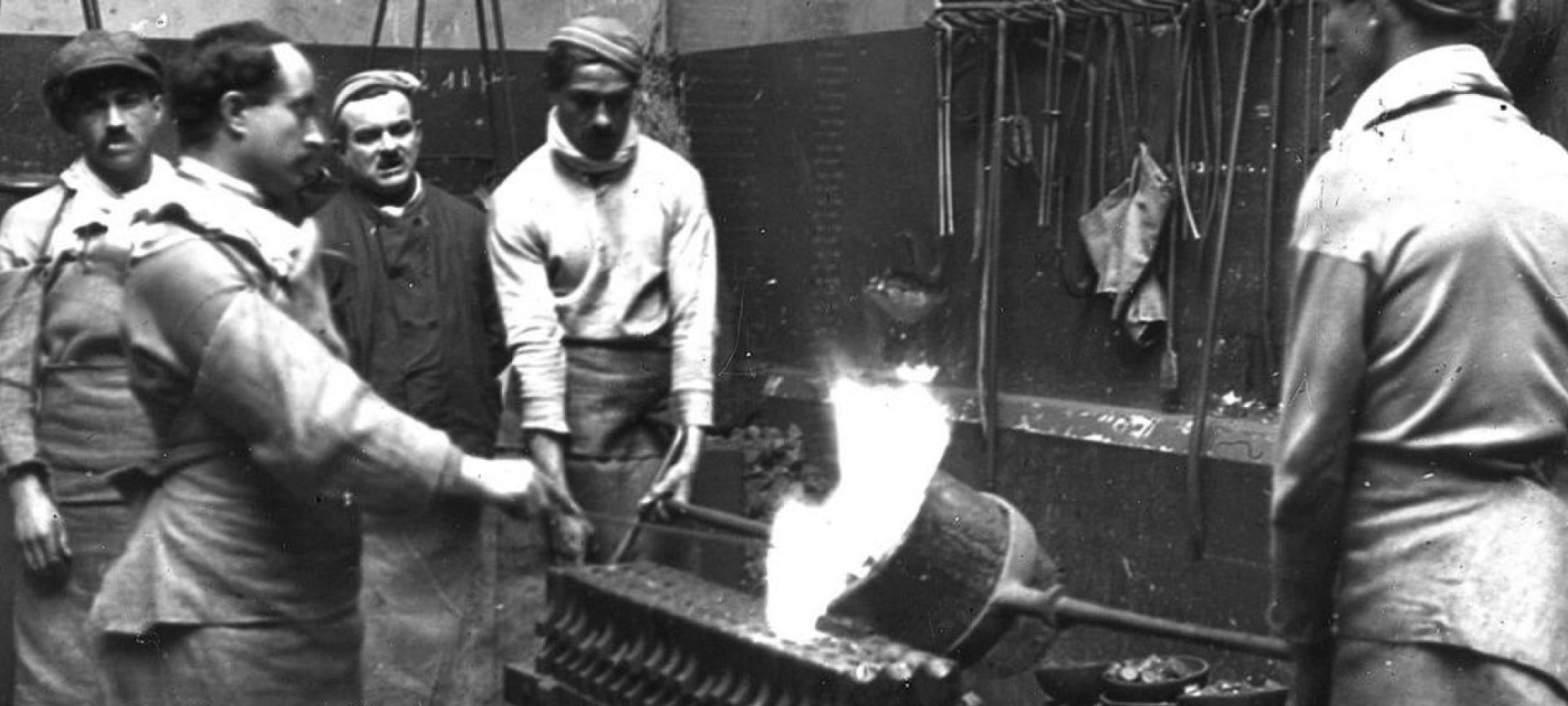
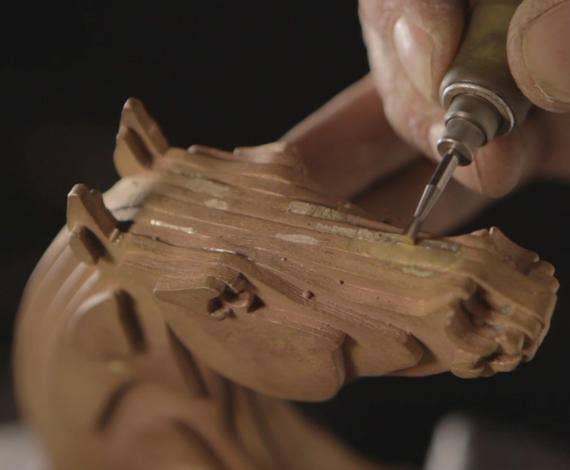
The foundry techniques
Lost wax melting has existed since 1500 B.C. and enables complex forms to be obtained. V-Process melting is another high quality process using vacuum moulding and developed in the 1970s. The chiseler stamps the piece, enabling it to be close to the original model by correcting the asperities of the raw foundry metal. The hot patina applier colours the metal according to a pallet of over 250 shades.
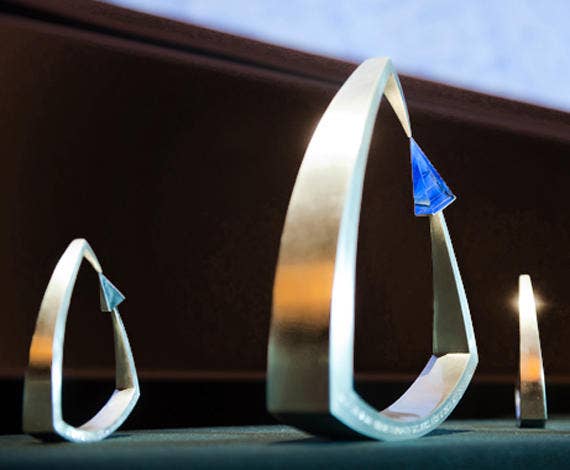
Producer and editor
Monnaie de Paris produces octuplets, limited editions and general public editions. The Art Foundry produces works
- manufactured in house;
- produced with an external artist;
- on behalf of clients, as editor.
The artist and the craftsmen collaborate to produce an artistic bronze faithful to the artistic desire, mastering the technical constraints.
Explore all the faces of Monnaie de Paris
-
-
Break into our plant in Pessac
Pessac plant strikes approximately 1 billion circulating coins at Pessac, half of it is for the export market
-
Online shop
Discover all our products
Buy online our latest collection ! Secured payment and fast shipping
-
Learn more about our craftmanhip
Thanks to their state-of-the-art know-how, our creative craftsmen shape precious ores, engrave style and time in metal and manufacture medals, awards, decorations...
-
Learn about our thousand year history
Monnaie de Paris is France's longest standing institution and one of the oldest enterprise in the world
-